October 20, 2020
Feature article – Key design considerations when applying subsea buoyancy to dynamic power cables on floating offshore wind foundations
The presence of greater wind reserves further offshore and the potential future shortage of shallow water locations, means floating offshore platform placement in deeper water is becoming more desirable.
Designing platforms and dynamic cable configurations for deeper water environments requires careful planning to ensure the longevity of the floating structures and the connecting power cables.
A variety of cable configurations can be produced with the application of discrete buoyancy modules placed at strategic intervals along the length of the cable. Selecting the correct buoyancy arrangement for the relevant conditions is critical to ensure cable loads and motions are managed and maintained within allowable limits.
A tried and tested method used to protect many subsea cable installations is a ‘lazy wave’ configuration, created using Distributed Buoyancy Modules (DBM) to support the cable in an arch-shaped formation to reduce cable tensions and displacements relative to the movement of the floating foundation.
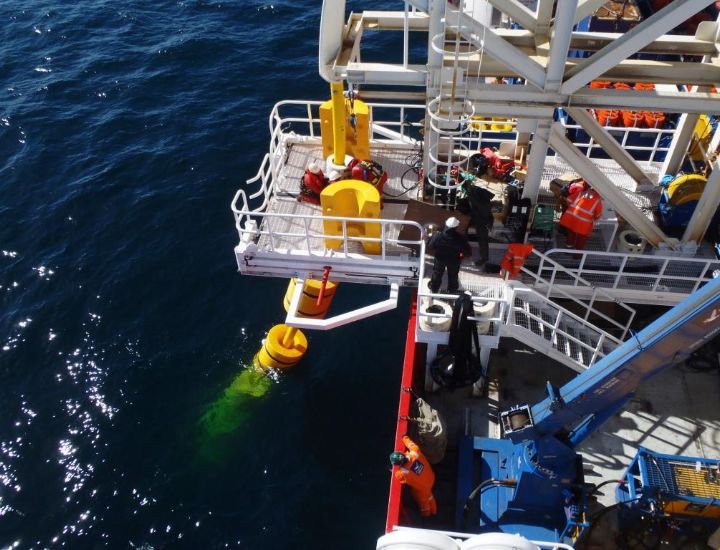
When attaching DBM to the cable, special consideration needs to be taken in the clamping design to build a level of compliance that copes with the variations in load and cable dimensions during the installation and operating period. This is necessary to ensure suitable clamping force is maintained on the cable to avoid slippage throughout the design life, whilst at the same time not over-utilising the cable.
Using dedicated installation tooling, these clamps can be installed within three to four minutes, enabling rapid on vessel deployment, resulting in significant time and cost savings offshore.
Another key consideration is the overall reliability of the buoyancy system providing the up thrust. Typically, to maintain the lazy wave configuration’s intended performance, buoyancy loss over the design life should be less than 5%. As the DBMs sit in mid-water, they will experience hydrostatic pressure; the deeper, the greater it is.
Polyurethane foam inside a sealed shell and steel tanks can be used close to sea level, however their long-term performance is reliant on the continued integrity of their outer shell. Syntactic foam is the most commonplace buoyancy system used in DBMs as, comprising of a composite foam containing graded pressure rated spheres, it is a self-contained system and not susceptible to catastrophic buoyancy loss due to holes or punctures in the surrounding shell.
These considerations are essential to maintain the buoyancy’s intended function of providing the lazy wave configuration that protects the cable.
Richard Beesley, Business Group Manager and Andy Smith, Sales Team Manager, CRP Subsea (formerly Trelleborg Offshore UK)